Kenworth News
Seattle University Students Help Optimize Weight for Kenworth
In the trucking industry, productivity and fuel efficiency are key ingredients for success. And, for those in weight sensitive applications, so is trimming weight from the truck. Simply, the more you can haul, the more you can make, and during the truck spec’ing process fleets want to know the impact that changing specs might have on overall weight.
“We often have large customers that have regional preferences for truck specs,” said Reid Nabarrete, Kenworth’s assistant chief engineer. “They might run in a mountainous area, so they’ll spec a bigger engine and different transmission – maybe even a different sleeper,” he said. “Then, another terminal might run the Midwest – where they don’t need as much horsepower and require different specs. We know the main weight difference between major components, but when spec’d, they have a cascading impact on all the subcomponents. That’s when the challenge begins in calculating weight.”
For Nabarrete and the Kenworth engineering team, those calculations typically mean hours of work to calculate weights – something they are able to do with an accuracy of close to plus or minus 2 percent. But, the idea of using Artificial Intelligence (AI), had been something the company has been looking at for several years. Using AI could speed the process and close the accuracy gap.
That’s where undergrad seniors in computer science came in from Seattle University. Kenworth has been working with Seattle U on real-world "Capstone" projects for more than 30 years. It’s part of a program in which senior year mechanical and electrical engineers, and in this case the undergrad senior students, from the school’s computer science department, participate in “Capstone” projects with local companies. Capstone enables students to put much of their knowledge to work in an academic yearlong class to create something tangible that one day might be commercially produced.
Top row, from left: Seattle University Professor Richard LeBlanc, Department of Computer Science and Software Engineering; and Seattle U. student Arjun Ramesh. Middle row, from left: Thomas Lee, Kenworth fleet sales technical manager and Kenworth liaison with Seattle University; and Seattle U. students Kai Hirose and Gavin Limchayseng. Front row: Nayif Alhomoud of Seattle U.
The four students built upon what worked and what didn’t work from other Seattle U students who took a run at using AI for Kenworth’s “weight optimization” a few years back. “The current team learned from the past, and during their school year were able to develop code, as well as AI learning code, to figure out weight from the thousands of trucks Kenworth built every year. With so many options that Kenworth offers to customers, there was a lot of data to process,” said Nabarrete.
Ultimately, the students came back with predictive modeling, based on AI, that was “incredibly accurate,” according to Nabarrete.
“When we audited their predictions, we found they were within 1 percent of our manual calculations. And, those were consistent calculations. So, a customer with a ‘standard’ truck weighing in at 16,000 pounds for example, could give us a list of spec changes, and the students could come within 160 pounds of the actual true build weight. And they could do it in minutes, not hours,” he said.
Nabarrete said this is a great example of giving students a tangible project that has the potential to impact business. “The students are all in when putting their skills to work in a meaningful project. We’re excited to work with and mentor them and see if their work can be taken to the next stage.”
While the Seattle U students have now graduated, and turned their tassels, their work is moving forward within Kenworth. “We plan to take what they’ve produced and refine it further,” said Nabarrete. “I fully expect we will be using AI in weight calculations with our customers or a regular basis in the very near future.”
While Seattle U students were working on weight, another group comprised of mechanical engineers, under Kenworth engineer Stan DeLizo’s leadership, were looking ahead to the future and exploring how to predict and compensate for handling while driving – something that could be used for driver assist automation, and eventually in autonomous vehicles.
“This project was especially challenging since the four students couldn’t collaborate in person – they had to interact via Zoom meetings,” said DeLizo. “We had a unique challenge for them, and they came through with a scale model prototype that could easily be translated into a full-scale Kenworth….and that’s where we will go next with their findings.”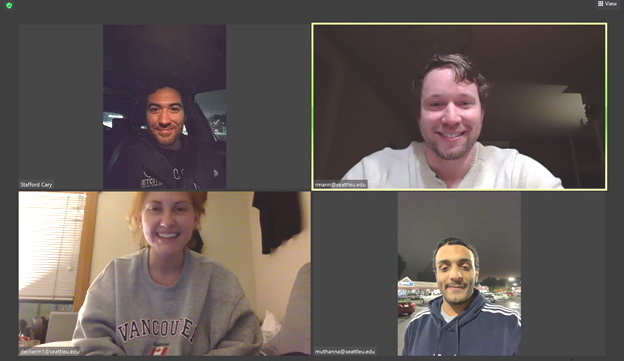
Shown during a Zoom call are members of the Kenworth - Seattle University Turn Prediction Project Team. From top left, clockwise, are Seattle University students Cary Stafford, Ryan Mann, Mohammed Abdulsalam and Meghan Decker.
According to DeLizo, who has been working with Seattle U students for 10 years on projects, the enthusiasm and ability of “young minds” to look at ideas without “tunnel vision” is always inspiring. “This is all new to them, so they look at all the options out there – using new technology and thinking outside the box,” he said. “In our project, they had a budget for equipment and set out to find sensors and cameras that would serve as the base for data input.”
The project’s goal was to emulate how a professional driver handles turns. “Humans see, anticipate and have an understanding of road conditions – if the road is slippery, or if there is gravel or something on the road ahead, they’ll make adjustments when cornering,” said DeLizo. “We’re trying to do that same thing through optical sensors surrounding the vehicle and trailer. Those sensors use image recognition and edge detection to inform the system of the truck’s actual location on the turn-path. Then, through mathematical modeling, which uses the vehicle’s known attributes, we’re able to predict the minimum radius turn path in each direction.”
In layperson’s terms, the project allows a Kenworth truck to automatically – and with a minimum turning radius – navigate a corner, or turn, safely.
Upon completion of a 1/10th scale model, equipped with sensors and cameras, the students provided an actual demo in front of Kenworth engineers. “To say we were very satisfied with their results and efforts would be an understatement,” said DeLizo with a smile. “What these students came up with is almost ready for bolting onto a full-size truck.”
Kenworth is The Driver’s Truck™. See what drivers are saying at www.kenworth.com/drivers.
Kenworth Truck Company is the manufacturer of The World’s Best® heavy and medium duty trucks. Kenworth’s Internet home page is at www.kenworth.com. Kenworth is a PACCAR company.
“We often have large customers that have regional preferences for truck specs,” said Reid Nabarrete, Kenworth’s assistant chief engineer. “They might run in a mountainous area, so they’ll spec a bigger engine and different transmission – maybe even a different sleeper,” he said. “Then, another terminal might run the Midwest – where they don’t need as much horsepower and require different specs. We know the main weight difference between major components, but when spec’d, they have a cascading impact on all the subcomponents. That’s when the challenge begins in calculating weight.”
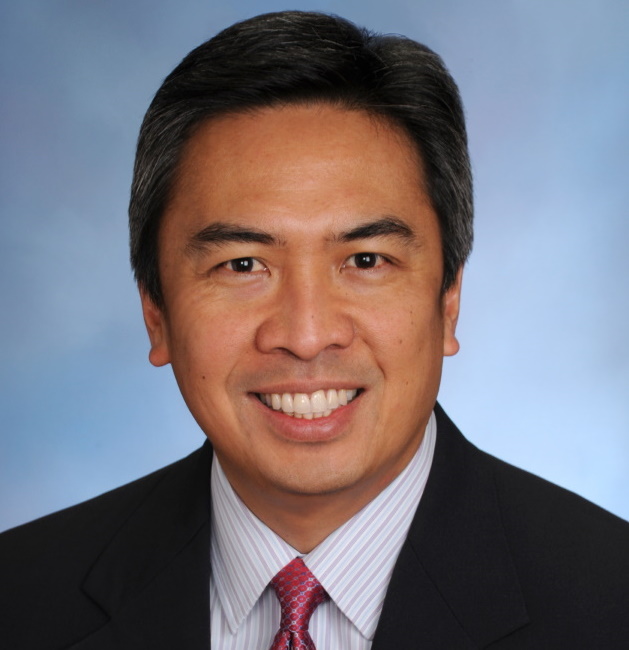
Reid Nabarrete
For Nabarrete and the Kenworth engineering team, those calculations typically mean hours of work to calculate weights – something they are able to do with an accuracy of close to plus or minus 2 percent. But, the idea of using Artificial Intelligence (AI), had been something the company has been looking at for several years. Using AI could speed the process and close the accuracy gap.
That’s where undergrad seniors in computer science came in from Seattle University. Kenworth has been working with Seattle U on real-world "Capstone" projects for more than 30 years. It’s part of a program in which senior year mechanical and electrical engineers, and in this case the undergrad senior students, from the school’s computer science department, participate in “Capstone” projects with local companies. Capstone enables students to put much of their knowledge to work in an academic yearlong class to create something tangible that one day might be commercially produced.
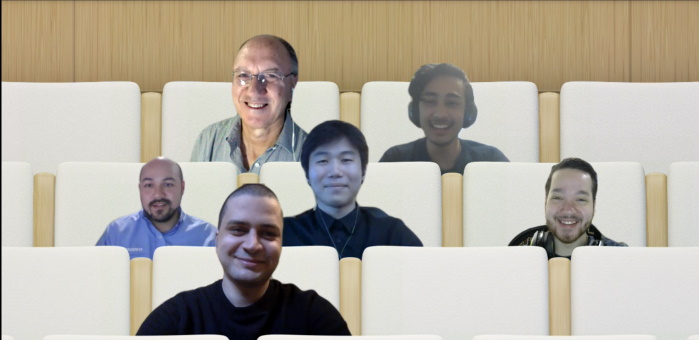
Kenworth – Seattle U Chassis Weight Optimization Team
Top row, from left: Seattle University Professor Richard LeBlanc, Department of Computer Science and Software Engineering; and Seattle U. student Arjun Ramesh. Middle row, from left: Thomas Lee, Kenworth fleet sales technical manager and Kenworth liaison with Seattle University; and Seattle U. students Kai Hirose and Gavin Limchayseng. Front row: Nayif Alhomoud of Seattle U.
The four students built upon what worked and what didn’t work from other Seattle U students who took a run at using AI for Kenworth’s “weight optimization” a few years back. “The current team learned from the past, and during their school year were able to develop code, as well as AI learning code, to figure out weight from the thousands of trucks Kenworth built every year. With so many options that Kenworth offers to customers, there was a lot of data to process,” said Nabarrete.
Ultimately, the students came back with predictive modeling, based on AI, that was “incredibly accurate,” according to Nabarrete.
“When we audited their predictions, we found they were within 1 percent of our manual calculations. And, those were consistent calculations. So, a customer with a ‘standard’ truck weighing in at 16,000 pounds for example, could give us a list of spec changes, and the students could come within 160 pounds of the actual true build weight. And they could do it in minutes, not hours,” he said.
Nabarrete said this is a great example of giving students a tangible project that has the potential to impact business. “The students are all in when putting their skills to work in a meaningful project. We’re excited to work with and mentor them and see if their work can be taken to the next stage.”
While the Seattle U students have now graduated, and turned their tassels, their work is moving forward within Kenworth. “We plan to take what they’ve produced and refine it further,” said Nabarrete. “I fully expect we will be using AI in weight calculations with our customers or a regular basis in the very near future.”
Driving the Truck of the Future?
While Seattle U students were working on weight, another group comprised of mechanical engineers, under Kenworth engineer Stan DeLizo’s leadership, were looking ahead to the future and exploring how to predict and compensate for handling while driving – something that could be used for driver assist automation, and eventually in autonomous vehicles.
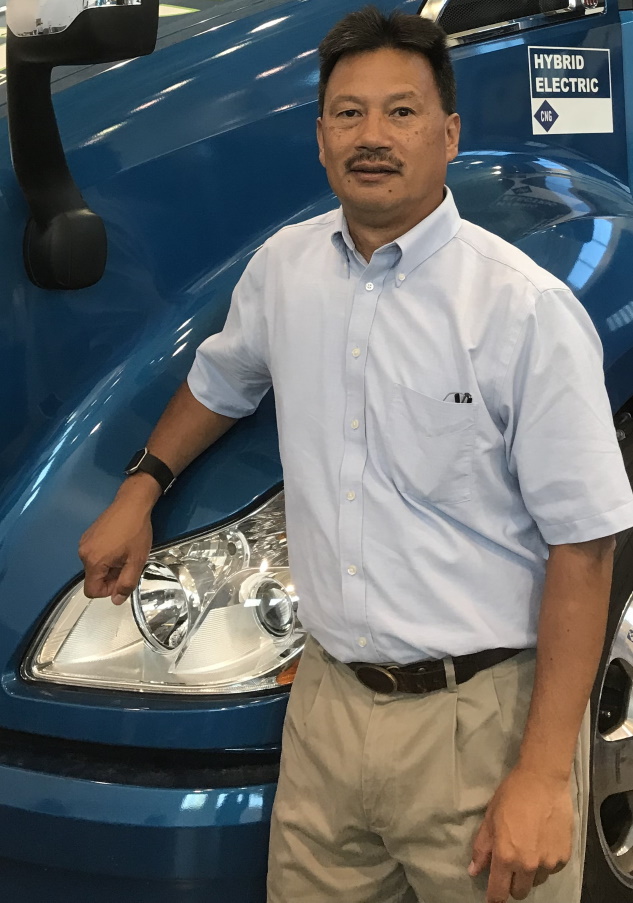
Stan DeLizo
“This project was especially challenging since the four students couldn’t collaborate in person – they had to interact via Zoom meetings,” said DeLizo. “We had a unique challenge for them, and they came through with a scale model prototype that could easily be translated into a full-scale Kenworth….and that’s where we will go next with their findings.”
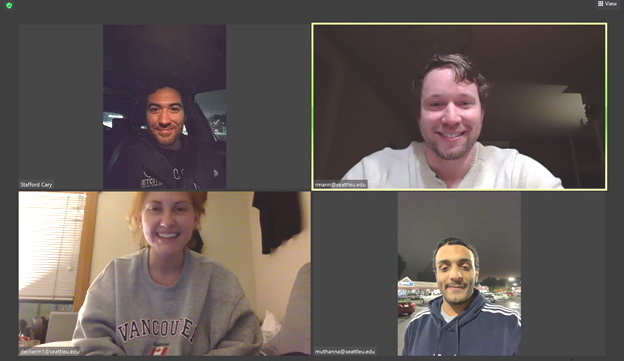
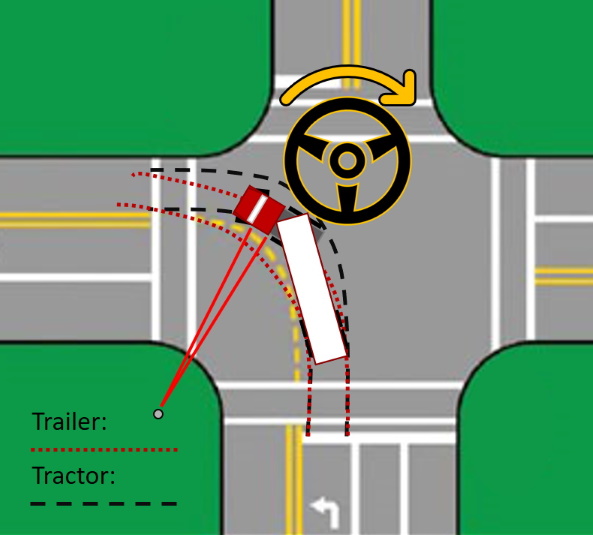
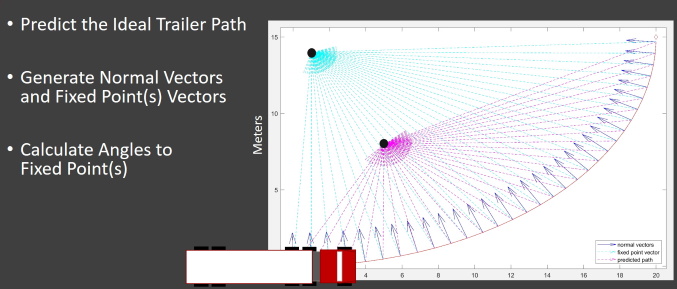
Kenworth is The Driver’s Truck™. See what drivers are saying at www.kenworth.com/drivers.
Kenworth Truck Company is the manufacturer of The World’s Best® heavy and medium duty trucks. Kenworth’s Internet home page is at www.kenworth.com. Kenworth is a PACCAR company.